三帝科技宗贵升博士:从3D打印出发,用数字科技升级制造
2023年6月10日,由中国经济传媒协会、浙江绍兴市政府联合主办,以“推进中国式现代化 高质量发展开新局”为主题的“2023中国经济传媒大会”在浙江绍兴召开,来自全国经济界、传媒界、企业界的数百名代表共聚一堂,解读当前经济形势与挑战,分析数字时代发展机遇,共话深度融合路径,凝聚推进中国式现代化、促进高质量发展的磅礴力量。在下午举办的“产业数字化:实体经济转型升级新引擎”经济论坛中,著名数字经济专家学者、企业嘉宾、媒体代表等,共同就推动实现实体产业与数字技术深度融合发展等话题进行了深入解读和研讨。北京三帝科技股份有限公司董事长、“2018中国经济新闻人物”宗贵升博士受邀在论坛中作了题为《从3D打印出发,用数字科技升级制造》的演讲,分享了3D打印在传统制造数字化转型升级中的重要应用,他指出,经过多年发展,3D打印已经成了数字化转型的一个重要利器。

当今全球发展的大趋势正改变着企业和个人的生活,其中,实业公司受“数字化、移动性、一切皆是服务”趋势的直接影响,而数字化技术推动传统制造业升级和制造服务化是这些大趋势影响实业的直接体现。近年来,3D打印数字化技术已经推动了铸造、注射成型、手板行业的数字化制造进展。制造工艺方法的变革也反映了数字化发展的大趋势:机械特征的等材制造,包括铸、锻、焊等,已经有近3000年的历史;自动化特征的减材铸造,包括车、铣、磨等,发展了近300年;而数字化特征的增材制造(即3D打印),包括选区激光熔融、选区激光固化、粘结剂喷射等,问世也已经30多年。3D打印与传统制造工艺的复合应用,正是制造产业数字化的重要部分。
3D打印数字化制造技术经过30多年的发展,其产业化应用全球年复合增长率在20%以上,中国甚至更高,但由于其产值基数相对较小,3D打印行业尽管意义重大,至今却还是个小行业。3D打印产业化缓慢的主要原因一是打印效率低,即制造速度慢;二是打印材料贵,即制造成本高。一个既慢又贵的技术,很难被应用到生产线中去,这就是为什么之前3D打印设备的主要用户大多是科研院所、大公司的研发部门、学校以及3D打印服务机构。为解决传统3D打印既慢又贵的问题,3D打印2.0粘结剂喷射工艺应运而起。采用了“线扫描”技术的3D打印2.0粘结剂喷射BJ工艺是一种高效率、高精度的增材制造技术,其沿用传统粉末冶金行业的材料体系和烧结工艺,成本低廉,材料标准化程度高,能够为工业界提供高效率、高质量、低成本的金属增材制造解决方案,可以应用到生产线,为3D打印技术的规模化应用打下了坚实基础。而随着3D打印应用领域的不断扩大,预计3D打印2.0更将为3D打印行业带来突破性持续增长,尤其是在助力传统制造升级方面,业绩将逐步显现。
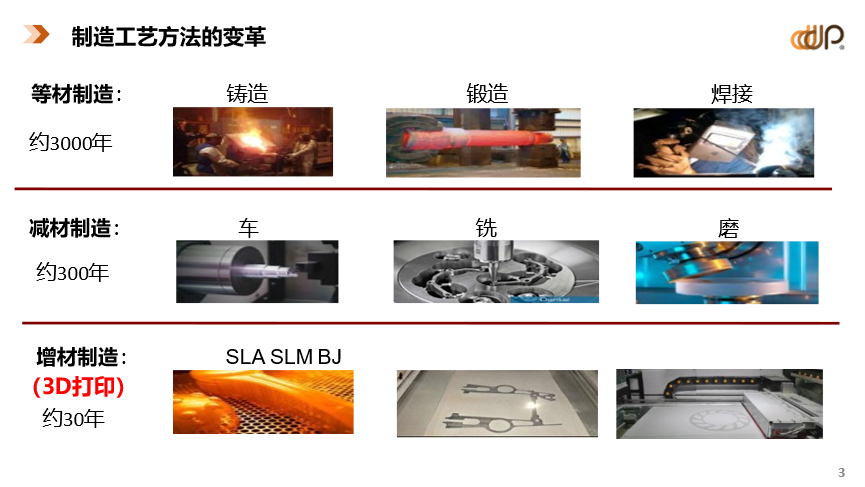
目前,全球3D打印市场在千亿规模基础上快速扩张。全球3D打印产业结构中3D打印服务占比最高,而中国市场3D打印设备占比最高,可见未来中国3D打印的应用市场潜力巨大。从中国机械制造的整体行业格局来看,等材制造市场过万亿,规模最大;减材制造市场在5000亿左右;而增材制造目前在300亿左右,但增长很快,尤其是3D打印2.0的出现,加速了复合制造(如增减、增锻减等)及数字化升级传统制造的节奏,千亿市场指日可待。以铸造行业为例。中国是世界铸造第一大国,有4000亿左右的市场规模,全球占比45%,有24000多家铸造厂,保持着稳健的增长,但存在高能耗、高污染、不强、不精的问题。为此,我国十四五规划指明了数字化升级等发展目标,提出要用3D打印来实现砂型铸造数字化、绿色化,建立200个以上的示范绿色铸造工厂。今年4月14日,工信部、发改委、环保部也联合发文,要推动一体化压铸成形、无模铸造、砂型3D打印等先进工艺技术实现产业化应用。
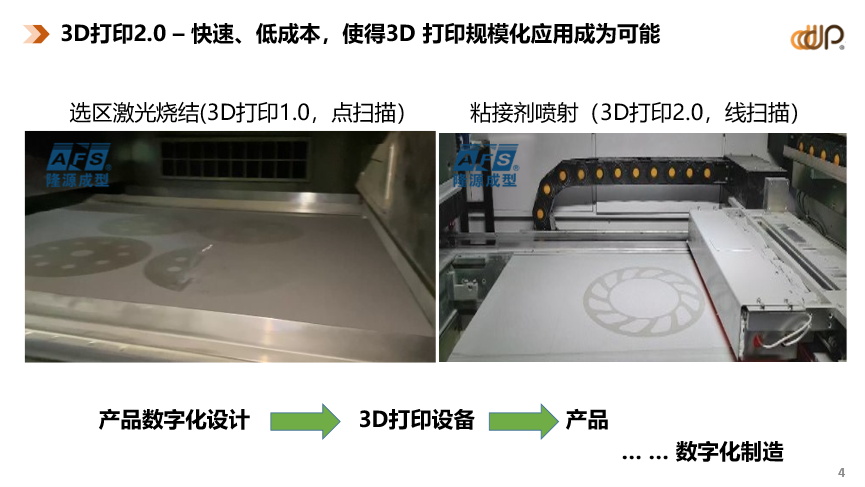
通过对铸造行业的分析,就更能深刻理解铸造业数值化升级的迫切性。有数据统计,全国铸件年产量万吨以上的铸造企业超过千家,5万吨以上的企业近200家。头部2000多家的铸件产量占全国总产能的55%以上。而头部企业缺乏定制能力或小批量试制能力,开发新产品速度慢、成本高;“长尾”企业产能利用率低,大多要被淘汰;只有“长尾”中的头部企业,在依靠3D打印和自动化率提升后能够生存,并可能有数倍的集中度提升空间。在这个转型升级的重大机遇下,三帝科技果断布局,在掌握了3D打印2.0核心设备、材料和工艺技术的基础上,通过并购铸造厂,直接打通了3D打印工艺和铸造工艺。同时,将3D打印2.0技术应用于提升粉末注塑成型,形成了3D打印数字化铸造和粉末冶金成型的竞争能力,成功创建多材料、全尺寸、全链路服务模式。目前客户包括中国航发、兵器集团、玉柴、吉利汽车等航空航天及军工、汽车等领域的头部企业,辐射机械制造领域众多客户,复购率高、成长性强。

当今全球发展的大趋势正改变着企业和个人的生活,其中,实业公司受“数字化、移动性、一切皆是服务”趋势的直接影响,而数字化技术推动传统制造业升级和制造服务化是这些大趋势影响实业的直接体现。近年来,3D打印数字化技术已经推动了铸造、注射成型、手板行业的数字化制造进展。制造工艺方法的变革也反映了数字化发展的大趋势:机械特征的等材制造,包括铸、锻、焊等,已经有近3000年的历史;自动化特征的减材铸造,包括车、铣、磨等,发展了近300年;而数字化特征的增材制造(即3D打印),包括选区激光熔融、选区激光固化、粘结剂喷射等,问世也已经30多年。3D打印与传统制造工艺的复合应用,正是制造产业数字化的重要部分。
3D打印数字化制造技术经过30多年的发展,其产业化应用全球年复合增长率在20%以上,中国甚至更高,但由于其产值基数相对较小,3D打印行业尽管意义重大,至今却还是个小行业。3D打印产业化缓慢的主要原因一是打印效率低,即制造速度慢;二是打印材料贵,即制造成本高。一个既慢又贵的技术,很难被应用到生产线中去,这就是为什么之前3D打印设备的主要用户大多是科研院所、大公司的研发部门、学校以及3D打印服务机构。为解决传统3D打印既慢又贵的问题,3D打印2.0粘结剂喷射工艺应运而起。采用了“线扫描”技术的3D打印2.0粘结剂喷射BJ工艺是一种高效率、高精度的增材制造技术,其沿用传统粉末冶金行业的材料体系和烧结工艺,成本低廉,材料标准化程度高,能够为工业界提供高效率、高质量、低成本的金属增材制造解决方案,可以应用到生产线,为3D打印技术的规模化应用打下了坚实基础。而随着3D打印应用领域的不断扩大,预计3D打印2.0更将为3D打印行业带来突破性持续增长,尤其是在助力传统制造升级方面,业绩将逐步显现。
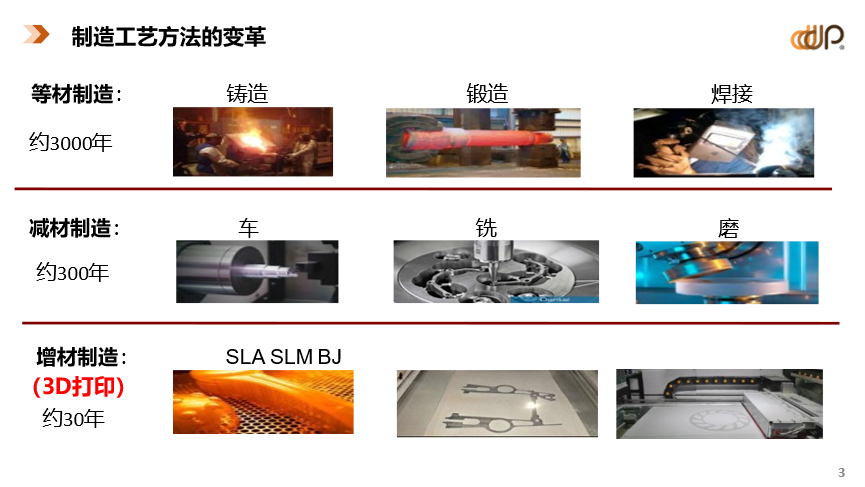
目前,全球3D打印市场在千亿规模基础上快速扩张。全球3D打印产业结构中3D打印服务占比最高,而中国市场3D打印设备占比最高,可见未来中国3D打印的应用市场潜力巨大。从中国机械制造的整体行业格局来看,等材制造市场过万亿,规模最大;减材制造市场在5000亿左右;而增材制造目前在300亿左右,但增长很快,尤其是3D打印2.0的出现,加速了复合制造(如增减、增锻减等)及数字化升级传统制造的节奏,千亿市场指日可待。以铸造行业为例。中国是世界铸造第一大国,有4000亿左右的市场规模,全球占比45%,有24000多家铸造厂,保持着稳健的增长,但存在高能耗、高污染、不强、不精的问题。为此,我国十四五规划指明了数字化升级等发展目标,提出要用3D打印来实现砂型铸造数字化、绿色化,建立200个以上的示范绿色铸造工厂。今年4月14日,工信部、发改委、环保部也联合发文,要推动一体化压铸成形、无模铸造、砂型3D打印等先进工艺技术实现产业化应用。
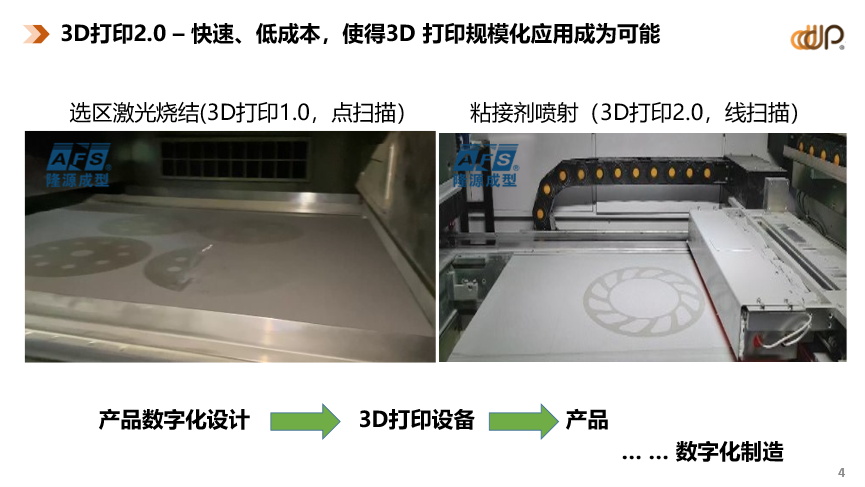
通过对铸造行业的分析,就更能深刻理解铸造业数值化升级的迫切性。有数据统计,全国铸件年产量万吨以上的铸造企业超过千家,5万吨以上的企业近200家。头部2000多家的铸件产量占全国总产能的55%以上。而头部企业缺乏定制能力或小批量试制能力,开发新产品速度慢、成本高;“长尾”企业产能利用率低,大多要被淘汰;只有“长尾”中的头部企业,在依靠3D打印和自动化率提升后能够生存,并可能有数倍的集中度提升空间。在这个转型升级的重大机遇下,三帝科技果断布局,在掌握了3D打印2.0核心设备、材料和工艺技术的基础上,通过并购铸造厂,直接打通了3D打印工艺和铸造工艺。同时,将3D打印2.0技术应用于提升粉末注塑成型,形成了3D打印数字化铸造和粉末冶金成型的竞争能力,成功创建多材料、全尺寸、全链路服务模式。目前客户包括中国航发、兵器集团、玉柴、吉利汽车等航空航天及军工、汽车等领域的头部企业,辐射机械制造领域众多客户,复购率高、成长性强。
3D打印数字化铸造,无需开模,从三维数据设计,到铸造模具直接打印,然后铸造,大幅缩短了新产品开发周期,降低了成本。采用了3D打印数字化工艺的铸造厂,其生产造型方式发生了变化,大幅降低了能耗和污染、改善了工作环境、提升了产品附件值和成品率,使得复杂件的快速、高精度、绿色铸造成为可能。比如汽车发动机缸体新品开发,传统铸造方式生产周期需要3-4个月,如果要修改,就要改模具甚至重开模具,耗时会更长。采用3DP砂型打印快速铸造,两周内交付铝合金成品铸件,如果要修改,也只需要修改数据,整体费用从百万元降至几万元。
随着3D打印2.0带来的打印效率的提升和成本的降低,3D打印在批量铸造应用的比重也将进一步扩大,3D打印技术将推动传统铸造升级成为绿色数字化快速铸造,并带动广大铸造企业转型升级。在论坛的圆桌对话环节,宗贵升博士与中国城市发展研究会、奇安信科技集团、NextHuman唯物科技等负责人,共同就产业数字化与实体经济深度融合发展模式与路径、数字经济重塑需求端下的产业结构优化升级、数字化转型中国方案探索等话题进行了畅谈与探讨。